From pv magazine 03/25
Bright winter sun warmed a cool morning into a pleasant day in Greenwood, South Carolina, despite the threat of rain. On the last day of January 2025, around 80 attendees including state and local representatives, and community leaders attended a modest event in the small city to mark a big achievement for U.S. solar.
The ribbon-cutting ceremony was for an ES Foundry solar cell production facility likely to be the nation’s largest – for now. Solar industry representatives, trade press, and ES Foundry customers toured manufacturing operations and saw crystalline silicon (c-Si) solar cells at various development stages.
“It couldn’t come at a better time, onshoring upstream component manufacturing is more important than ever,” said Elissa Pierce, a solar supply chain analyst at Wood Mackenzie. She said “more than a dozen” solar module factories have been established since the IRA became law in 2022. ES Foundry is only the second c-Si cell fab and WoodMac anticipates reaching 11.3 GW of annual U.S. cell manufacturing capacity this year.
Thin-film dominance
U.S. solar manufacturing is dominated by First Solar, the cadmium telluride (CdTe) thin-film manufacturer based in Tempe, Arizona. Its monolithic production process involves glass going in one end of the production line and a finished module coming out the other.
In its third-quarter 2024 earnings call, First Solar CEO Mark Widmar confirmed the start of production at the company’s 3.5 GW, $1.1 billion factory in Alabama. First Solar is on track for 14 GW of US module output in 2026, and 25 GW globally, said Widmar.
Thin-film production is housed under one roof, but c-Si supply chains can be disparate. The crystalline silicon supply chain involves production of polysilicon feedstock plus solar ingots, wafers, cells, and modules separately. U.S. cell production still lags far behind the 50 GW of module capacity analyst Exawatt expects in 2025. There is, as yet, no U.S. wafer production.
“The companies we know that have brought wafers into the U.S. are Suniva and ES Foundry, Hanwha has brought wafers in, and Silfab brought some wafers in in January this year,” said Alex Barrows, head of solar at CRU-owned Exawatt. He estimates that, of 42 GW of announced cell manufacturing plans, 10 GW could come online this year, rising to 19 GW in 2026.
Cell production
Recapitalized Suniva started to bring 1 GW of cell production capacity online in the state of Georgia in mid 2024. Canada’s Silfab is also ramping a 1 GW line in South Carolina and has signed offtake agreements beginning in the second quarter of 2025. ES Foundry unveiled its 1 GW line in January and began cell shipments the following month. Suniva raised $110 million in October 2023, to restart cell production, and Silfab raised $100 million for cell operations in November 2024.
“We have a capacity of 1 GW by August and we will plan to reach 3 GW nameplate capacity,” said ES Foundry Chief Executive Alex Zhu, who has led U.S. operations for companies including Suntech, Shunfeng International Clean Energy and GCL System Integration. ES Foundry’s South Carolina cell fab is equipped for large-format, “G12” (210 mm) wafers but is currently using smaller “M10” (182 mm) materials. “For actual output, because we are using M10 right now, you probably have to discount like 15% to 20% from the nameplate [capacity],” said the CEO. ES Foundry intends to switch to G12 wafer production in its second expansion phase.
Cell drivers
The expansion of U.S. solar manufacturing capability has been driven by trade barriers and domestic incentives. For developers, these policies have made domestically produced PV modules attractive both in terms of security of supply and by virtue of attractive subsidies. However, the current policy upheaval caused by the Trump administration has caused a peak in uncertainty. The industry has been left to ponder what shape these measures will take in the future.
“I think almost the whole industry is waiting to see how the Trump government is working out, what details they change on the IRA is important,” said Zhu.
Cell producers are currently incentivized through the Inflation Reduction Act (IRA) by a tax credit of $0.04/W. There is an additional domestic content bonus tied to a 30% Investment Tax Credit (ITC), plus a further 10% if certain quotas of US-made components are incorporated into a utility-scale solar project. Both measures are important, according to Zhu, however, the ITC remains the most important measure for the U.S. solar industry as a whole.
Zhu said if the ITC is wound up or reduced early, then the impact to developers and manufacturers would be profound. “That would significantly alter the whole investment in the industry. There are so many options that are on the table, it’s difficult to predict. Of course, we will want to keep the 45X or keep the domestic content.”
Domestic content
It’s plausible that under Trump, very large domestic content requirements could be introduced for U.S.-made products to qualify for the ITC. This could be a positive for cell makers, but policy changes bring risk.
“A big issue that these cell factories have is raising capital,” said Pol Lezcano, a U.S. solar analyst and senior associate at BloombergNEF. He said that even before the 2024 election win, the prospect of a second Trump term had affected capital market attitudes toward solar investment. “Not only does it freeze capital, it also adds a layer of upstream supply risk – because you don’t know how harsh Trump will go after upstream components with ties to China.”
While the expansion in cell capacity is encouraging, Lezcano said producers remain heavily dependent on imports of upstream components such as wafers, ingots and polysilicon. A trade war, with potential to include Southeast Asian-based producers, could have a devastating effect. Marginal solar cell manufacturing projects appear increasingly unlikely by the day.
Serious investment
Sizable financing is required to establish U.S. cell production. PV technologist Peter Fath, the chief executive of manufacturing consultancy RCT Solutions, estimates that a “fully built-out” solar cell fab requires three times the capital expenditure (capex) of a module facility with the same level of automation. When things like the construction of a clean room and full utility costs are included, capex requirements can spiral to four or even five times higher than an equivalent module line.
“In the USA, to set up a cell factory is really a pain. Construction companies are taking whatever they can, and the same with utility companies,” said Fath. He added that obtaining Underwriters Laboratories (UL) certification for the production equipment and line can increase upfront costs by up to 20%. This could be a penalty for Chinese equipment suppliers in particular, who may not have cleared that hurdle yet.
Amid policy uncertainty, the potential for export controls on Chinese PV cell equipment bound for the United States has also caused concern. In early 2024, there were reports that the Chinese government would introduce restrictions in retaliation against U.S. trade barriers on module imports from China. However, industry analysts report that import data shows controls on equipment have not been imposed, at least in the current first wave of cell capacity investment.
Upstream supply
Sourcing other upstream materials may be problematic. Lezcano said there might be no end in sight for US manufacturers – with potential for new bottlenecks along the supply chain. “Everyone wants to get their hands on non-Chinese polysilicon, and Wacker, Hemlock and OCI can charge a premium. If you are trying to produce U.S. wafers, you are competing against a long list of companies.”
The decision to halt production at REC Silicon’s Moses Lake facility is not only a blow to non-Chinese polysilicon stocks, it may have also given pause to Hanwha Qcells. The manufacturer had ambitious cell production plans, but Lezcano said a proposed 3.3 GW, fully integrated production facility in Georgia could be delayed as a result.
“It was quite an investment made by Hanwha, the parent company – quite a big bet. Internally [the fact that] the deal didn’t work out may be causing management delays,” said Lezcano.
Qcells appears to have fallen behind schedule in commissioning its U.S. cell lines. Manufacturer and project developer Canadian Solar may also leave customers waiting for new cells from its $800 million, 5 GW facility in Indiana, announced in October 2023.
Despite subsidies and supportive trade measures, the route to success in crystalline silicon manufacturing in the United States remains difficult to navigate. Silfab hopes to use the negatively-doped, “n-type” cells it produces in both its rooftop and utility-scale module products, and Suniva is also supplying to third-party module makers. ES Foundry is trying to master cell production before considering joining the crowded module marketplace.
Unlike Europe, which remains overwhelmingly reliant on Chinese imports to supply its solar projects and installers, the United States is heading towards an onshoring milestone. Exawatt’s Barrows said import data for February or March is likely to reveal U.S. manufacturers supplying more than 50% of end market demand in the country – if only for modules at this stage.
“You will be able to see from the import data pretty soon that the U.S. will have shifted from a market that almost totally imports modules, something like a year or so ago, to a market that predominantly imports cells – but still imports some modules.”
[Editor’s note: Since this article was written, Mission Solar announced a solar cell factory in Texas anticipated to produce 1 GW by Q1 2026.]
Popular content
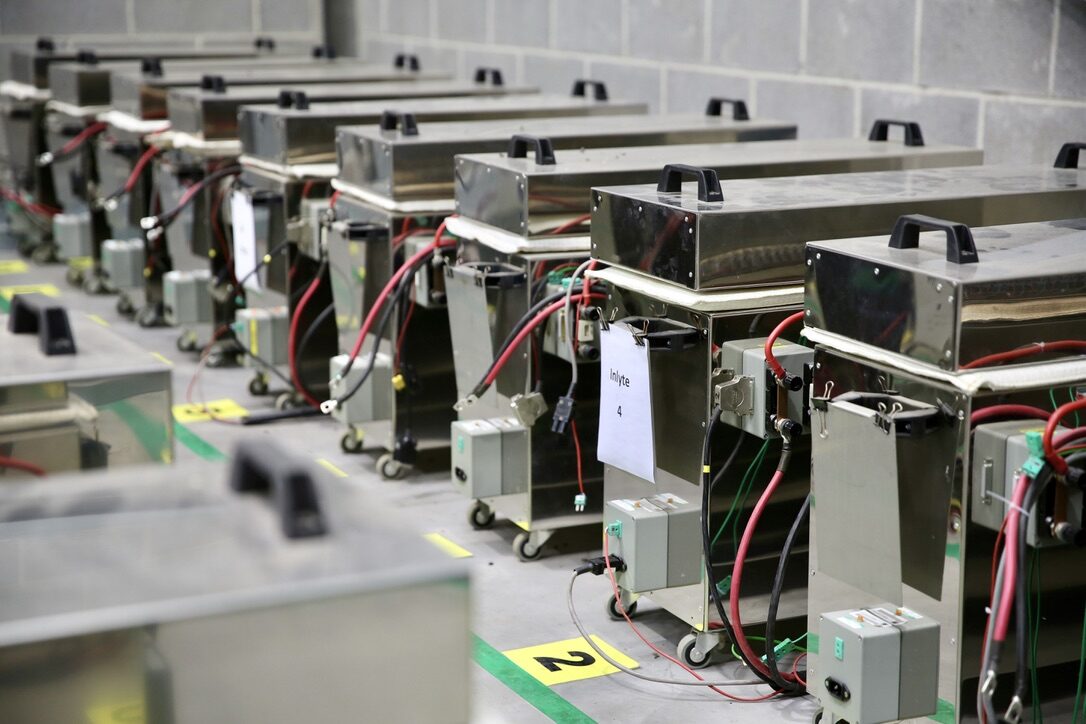