The U.S. government has set a target of a 50% reduction in greenhouse gas emissions by 2030. A recent report by ACORE and Clean Energy Associates (CEA) says that many recent models suggest that we’ll need 500 GW of cumulative PV installations by 2030 to achieve that goal. The Inflation Reduction Act (IRA) has stimulated tremendous growth in manufacturing but is it enough to meet our goals?
According to the Solar Energy Industry Association (SEIA) a record-setting 11 GW of new solar module manufacturing capacity came online in the United States during the first quarter, or a recording setting 71% increase. But to really onshore the solar supply chain, we need to step up the pace on cells, wafer, ingots and polysilicon. We need a balanced supply chain for many reasons, not the least of which John Smirnow emphasized in his keynote, which is national security.
On Day Three of pv magazine USA Week, four solar experts explored these forces while taking a deep dive into what the domestic manufacturing landscape looks like and what we can expect in the near future.
Panelists include Michael Carr, executive director of the Solar Energy Manufacturing for America Coalition, C.J. Colavito, vice president of engineering at Standard Solar, Christian Roselund, senior policy analyst at Clean Energy Associates and Craig Walker, sales manager USA at Soltec Trackers, North America.
In discussing how much capacity is actually being built versus announced and where the gaps are, Christian Roselund noted that CEA tracks which factories are bringing in the manufacturing machinery.
He said for near term capacity module factories are ramping up to the extent that we will have the re ramping up we are going to have the capacity to meet our needs.
“When we look at the cell side, there’s a big lag,” he said, noting that CEA is looking at just one cell factory that’s currently ramping up. However, others are importing manufacturing equipment, which CEA sees as promising in the 2026 timeframe.
Two ingot and wafer factories have been announced but with no projection as to capacity. Roselund said that for the near term CEA is expecting 8 GW of ingot and wafer, and ramp up will be slow because ingot and wafer manufacturing is the hardest part of the supply chain. He summarized that they’re more capital intensive, have a longer lead time, and present greater technical challenge than module manufacturing.
At the top of the solar supply chain is polysilicon, which eventually the U.S. will have plenty of thanks to Section 48D from the CHIPS Act that allows up to 25% Investment Tax Credit for ingot and wafer manufacturing. “Keep in mind that if you’re not importing equipment now, you’re probably not going to be manufacturing before the end of next year,” Roselund said, adding that “We’ll have these significant gaps for the next two years.”
Scaling up
The incentives within the IRA unlock the possibilities scaling up the supply chain. “Build fast and build big,” Carr noted is what the supportive policies including 48D are doing for the industry. The supportive policies that are now in place can work together to incentive not only growth, but scale, said Carr.
“The future is quite bright for building out the supply chain in the United States… it’s a matter of commitment,” Carr said.
Domestic content
The domestic content adder has received much attention, especially in light of the build out the U.S. supply chain, however, the panelists agreed that it is not currently possible to build a utility-scale solar plant that qualifies for the domestic content adder.
The first sector where projects will quality for domestic content will be in rooftop mounted PV, which Colavito said can be done in early 2025 with domestically produced racking and inverters and module-level power electronics. “Fixed tilt ground mount won’t be happening until we can get a domestic cell and we need to be confident that we can get that because according to the safe harbor percentages, 49% of the value comes from the cell,” said Colavito. “Without it you’re dead in the water,” he added.
It is encouraging that the cell capacity will be online before the end of 2026 to serve the distributed generation markets, according to Colavito. He added that the value of the domestic content bonus to distributed generation and community solar is two to four times more the value to utility-scale solar. “We can pay the premiums because it still delivers better energy rates to our customers and better return on investment to our lending partners.”
Aside from securing the domestic content adder, there are several benefits to U.S. manufactured goods. Soltec’s Craig Walker said that the tracker manufacturer won’t have a 100% U.S.-made product until Q3 2025; however, he said there are three reasons that it’s critical for them to be making products in the U.S., even if not qualifying for the adder. While only about 20% of its customers requesting 100% domestic content at this time, Walker said that Soltec is finding that lead times in the U.S. are so good it can compensate, depending on the milestones in the project.
Walker noted that buying U.S. made alleviates the insecurity that comes form any sort of imported content whether caused by political situations, natural disasters or supply chain problems abroad. “These three kay factors are pushing us more and more toward U.S. manufacturing, the only problem we face right now is price,” said Walker.
Looking at other components of the supply chain, Roseland noted that there are qualifications that should be made around capacity. U.S. made inverters are available, he said, but it’s going to be expensive and it depends on how many you need. Aluminum frames are also a challenge because they’re so much more expensive to make in the U.S. and some companies are going with steel frames. He said CEA is optimistic about the domestic supply of backsheets and encapsulants as they see more coming online in the U.S. “By the middle of next year the picture will have changed significantly, with the exception of big inverters,” Roselund said. He noted that microinverters are made in the U.S. now, but U.S. manufacturing of inverters for utility-scale has not yet scaled to capacity.
Carr said domestic content approach is very new and since the Department of Treasury has “zero experience in this area, they’ve had to get up to speed very quickly.”
“ We haven’t done industrial policy in this country in fifty years, so it’s not surprising that muscles may have atrophied somewhat,” Carr said. He suggested that some pieces may need to be changed at the statutory level, for example, incentivizing things like junction boxes “is not the way you’d design a strategic set of investments.” What’s important, Carr said, is to focus on modules, cells and wafers and “maybe not the other pieces that are not strategically important.”
“We have industrial policy and it’s clearly effective, but we’re stumbling over the details,” Roselund said. For example, the domestic content guidance is expected to be changed again, which creates a challenge. “Hopefully we can get this done where this is clear and predictable,” Roselund concluded.
Trade challenges
A preliminary decision was announced on countervailing duties and a decision is expected soon on anti-dumping. These tariffs relate to imports of crystalline silicon cells and modules from four Southeast Asian countries. While there is uncertainty around final details, SEIA expects the impacts to be modest. But what’s needed, Carr said, is continued certainty on the incentive and investment side. “Trade continues to be a whack-a-mole problem.”
Workforce
One of the biggest challenges to building out the manufacturing workforce in the U.S. According to an E2 report, over 42,000 clean energy manufacturing jobs have been added this year.
Carr noted that jobs are often anchors for communities and there’s a sense of pride and emotional response to manufacturing jobs. Manufacturing jobs are a career opportunity for people, and they can climb the ranks and build a middle class lifestyle. Particularly in counties that have suffered the brunt of losing manufacturing over the past few decades. These areas have the facilities and infrastructure, and now a new level of manufacturing is coming in and bringing a lot of pride. As John Smirnow noted in his keynote, every manufacturing job supports another seven jobs in the community. Carr noted that this “spin-off effect” is is the biggest contributor to the bright future we see. “It’s going to generate the stories and continued interest in pushing this forward.”
Bipartisan appeal
The tax credits are remarkably durable due to the jobs they’re bringing to red states, Roselund noted, adding that it’s telling that 18 Republican members of Congress wrote a letter tell House leadership not to touch the ITC. “While they didn’t vote for them they have recognized that the tax credits are supporting their constituents’ communities.”
Popular content
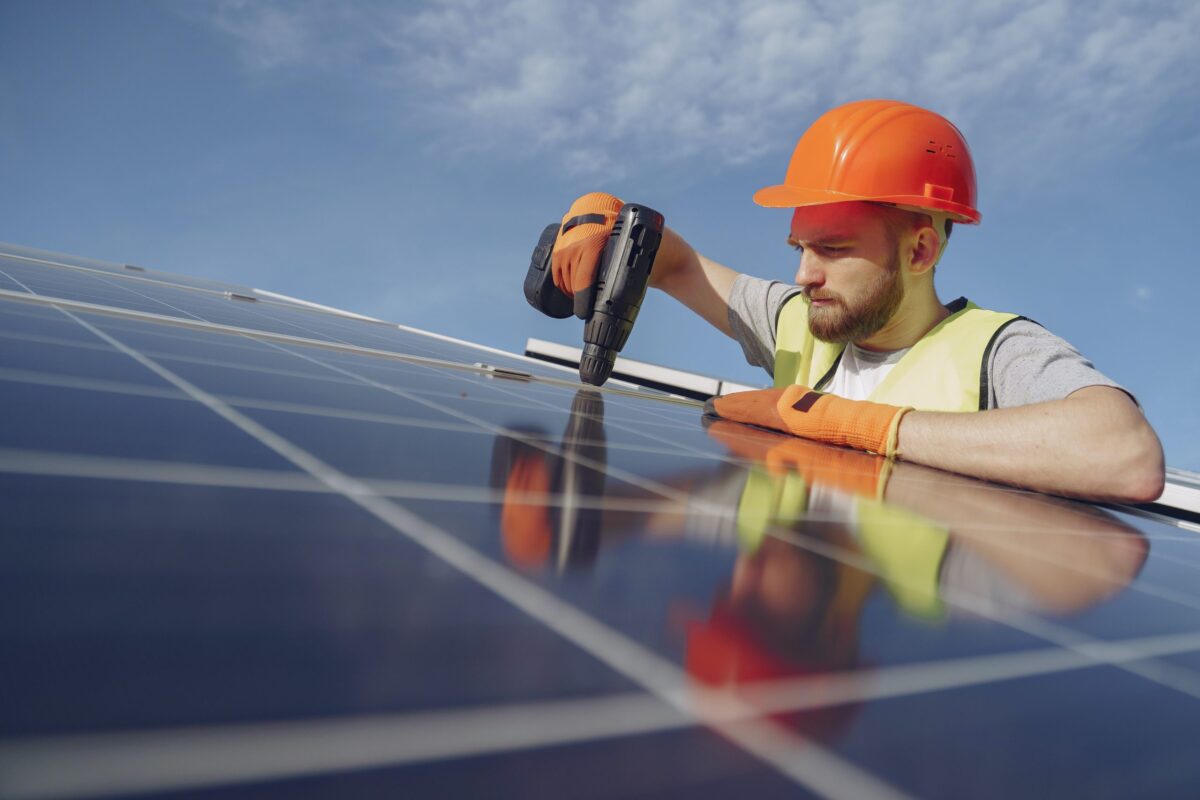