Automation continues to transform solar construction sites. Previously, we looked at O&M and site prep solutions. In this installment, we’ll highlight innovative robotic installation technology that is improving efficiency and quality for larger scale solar projects.
Terabase Energy unveiled its Terafab automated construction system in May. The new digital field factory solution aims to increase installation productivity for solar power plant construction by a factor of 2x over traditional methods. And in July, the company received a $25 million investment to support the commercial scale-up of the Terafab solution, bringing its total funding to more than $70 million to date.
Terabase CEO and cofounder Matt Campbell has been looking at solar construction automation for a long time. It started with cleaning robots and then offsite prefabrication solutions when he was with SunPower. About five years ago, Terabase spun out of SunPower to focus on automation technology.
The Terafab concept brings pre-fabrication to the jobsite to assemble PV panels and trackers to speed up installation time and reduce safety risks.
“It’s fairly straightforward,” Campbell explains. “We have a pop-up factory, which takes a day to install, and in the factory we bring in all the steel components, the torque tubes, panels and modules, and a robot unpacks and assembles it all on the assembly line. The line is eight modules long, and once a section is complete, it goes onto a delivery rover to be installed in the field every four minutes.”
A highspeed data network is deployed onsite to enhance communication between the robots, rovers and personnel.
“We’re trying to build faster, trying to build more efficiently, and we’re trying to improve safety,” Campbell says. “We’re also looking to lower the environmental footprint of solar jobsites, using electric machines, rather than diesel, and eliminating micro trash onsite. We’re looking to drive quality and CapEx savings through automation.”
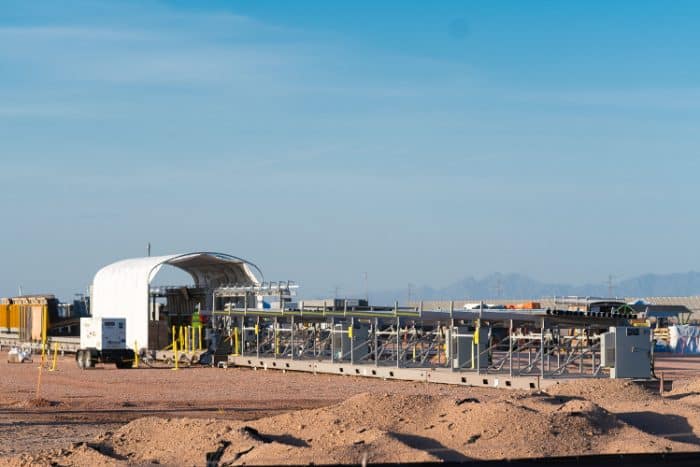
Worker safety was a big factor in developing the Terafab system, Campbell adds. To avoid extreme heat, the field factory is under a tent with fans and misters to keep people cool. Whereas many projects in the United States are moving to nighttime operations because of heat, the Terafab system allows projects to run 24/7.
Terabase opened a factory at the beginning of 2023 to build more of its digital field factories. It has built four so far.
Terafab beta was deployed on a 10 MW subset of a 400 MW jobsite in Texas last summer. The company’s first commercial deployment just wrapped up on a 17 MW portion of a 225 MW project in Arizona, in collaboration with developer Leeward Renewable Energy and EPC contractor RES.
Terafab is designed for solar projects of 50 MW and above, primarily in the utility-scale sector. However, Campbell says that the company may look at some C&I projects in the future as the technology becomes more nimble and costs are driven down.
Two factors drove the need for the Terafab solution, Campbell says: workforce shortages and increased panel sizes.
“There is a shortage of people in the solar industry, in every area from project management to construction labor. We have a chronic shortage, and it’s only going to get worse,” he says. “We’re only expecting more solar projects to be developed, and tools like this will help the industry to do things faster and more efficiently.”
Campbell adds that sometimes there is a concern that automation is going to kill jobs. However, he gives the example of the hydraulic excavator.
“People used to dig holes with shovels,” he says. “Now, with excavators they’re able to do that job more efficiently and safer.”
With solar panels continuing to increase in size, Campbell says that they are becoming harder and harder for humans to safely install by hand.
“Panels are 40% bigger than panels just three years ago,” he says. “Imagine the ergonomics to pick up and hold one of those over your head. People often cite the OSHA regulation that says a person can carry 50 lbs, so that means two people can carry 100 lbs. But that regulation is for a one-time lift. They’re not thinking of having to bend, lift and hold that weight. Worker health and safety important. In the future, there’s going to be more pressure to make panels bigger because it’s cheaper to manufacture.”
Campbell estimates that a worker could be lifting up to 10,000 lbs during a shift, installing panel after panel by hand.
“Everything in our industry is designed to be manually built,” he says. “It’s tough work, and some people will say, ‘suck it up.’ I think that’s a bit irresponsible.”
Automation makes the work better and safer for workers, Campbell argues. Improving those conditions could help reduce the current high turnover rate in the industry.
The Terafab system requires 10 factory workers and eight rover drivers. While people are still needed in the field to bolt everything together, they’re not required to perform heavy lifting.
The biggest challenge to bringing the Terafab solution to market, Campbell says, was adapting to the outdoor elements.
“Automation is easy when you’re inside a traditional factory, where it’s always 61 degrees and there’s no bee’s nest. In our beta deployment, we had major thunderstorms. It was an uncontrolled environment. Automation wants to be in a controlled environment.”
Another challenge was being able to match the production and efficiency of skilled project installers.
“EPCs are very efficient,” Campbell says. “We have to match the efficiency of traditional methods right out the gate or surpass them to be viable.”
While Terabase has already deployed its beta project, and its first commercial project is underway, these were on subsets of larger solar projects. Campbell says the company expects to scale up to build whole projects by the end of next year.
“We’re a bit conservative,” he says. “We have to get things perfected and get everything dialed in before we scale. Sometimes when a technology is scaled too early, it costs a lot money when you get it wrong.”
Terafab is currently being deployed with Nextracker mounting and First Solar Series 7 panels, and Terabase is working with the companies to recycle all packaging. In future, Campbell says Terafab will be compatible with different modules and trackers, but the company will remain limited on the number of different components supported to save on costs.
Campbell sees Terafab as a complement to expertise in the field.
“What’s being automated is the lowest skill position jobs,” he says. “It’s the backbreaking work that’s becoming more efficient. The other thing is it’s creating new kinds of jobs for the industry, such as rover drivers, technicians to maintain the equipment, and assembly line workers.”
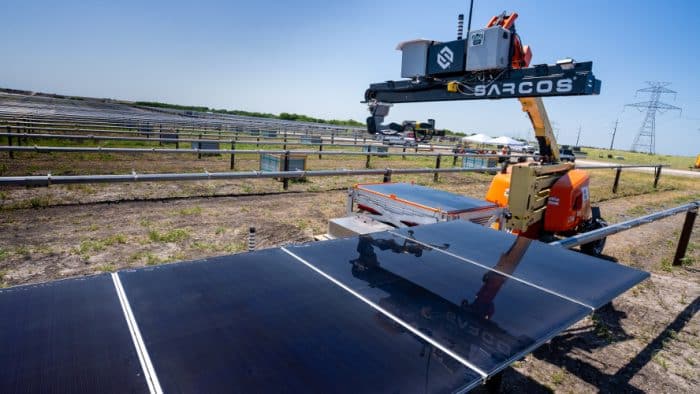
Sarcos robotics improve installations
Sarcos is a manufacturer that has been in the robotics industry for decades, according to senior VP Matt Vogt. The company’s entry into the solar industry came in 2021 with the Sarcos Outdoor Autonomous Manipulation of Photovoltaic Panels (O-AMPP) project, which is funded through the U.S. Department of Energy Solar Energy Technologies Office (SETO).
The system uses cameras and sensors to detect where the PV panel is and where it needs to go. Then, an autonomous arm picks up the panel using a vacuum lift system and places it in the approximate location, where a worker performs the final installation. The robotic arm goes into a gravity compensation mode to allow the worker to easily make any final alignment adjustments before attaching the PV panel to the clamps. Safety sensors help keep the worker safe, and the installation process takes about 30 seconds per panel.
“The goal was to streamline the process of installing solar panels through a harmonized robotics system,” Vogt says. “It’s been a two-year process. We’re looking to provide companies the ability to engage in more projects with a technology that improves their timeline and improves quality. It also helps reduce risk on the jobsite, such problems as lift fatigue.”
Sarcos completed its final validation field trial of the O-AMPP technology in March. In July, the company announced a partnership with renewable energy services provider Blattner Co. to further develop the robotics technology.
“The partnership allows us to further refine our technology,” Vogt says. “We’ll be conducting a series of field trials to get us to the next step in where we need to go. We’ll look at performance in various environmental conditions associated with solar sites, and Blattner has a number of options for us to conduct tests.”
After ticking off those boxes to ensure the technology delivers on its promise to improve jobsite safety, installation speed and overall quality, Sarcos is targeting late 2024 for the commercial launch of its O-AMPP solution.
Vogt believes that manpower is the single biggest driver for automation technology on solar jobsites.
“The activity of installing solar fields to this point has been very manual, involving heavy lifting and some extreme heat and extreme cold,” Vogt says. “Humans are expected to lift 70-80 lbs. We’ve seen estimates of an additional 7,000 to 8,000 people needed to complete the work that is forecasted in the solar industry. Our data shows a 5% year-over-year decline in the workforce. So you have an increase in the global demand for solar, but a decline in the number of workers. This is a technology that is specifically designed to decrease that concern.”
Vogt points to some “brutal” working conditions on solar jobsites, where temperatures can reach 110 degrees, and workers require a cooldown period after every 45 minutes of installation work. Automation can alleviate the impact on productivity in extreme conditions where solar projects typically are located.
In addition to offsetting the workforce shortage, Vogt adds that automation technology’s biggest benefit is improved installation speed and quality.
“Our data shows that a standard two-year project installation could be reduced to 18 months if the Sarcos system is used,” he says. “That’s about a 25% reduction in cost. If we can reduce the installation time by 25%, then there is a direct cost savings on that front.”
Despite still conducting final tests, Vogt says the biggest challenge to bringing the Sarcos O-AMPP system to market has been speed.
“Certainly, there are technology challenges, which are always there when trying bring a solution to market,” he says. “Our biggest challenge is do it more quickly. We’re trying to accelerate what is complicated development to meet demand. There is a lot of demand out there, so our biggest challenge is speed to market.”
Vogt expects AI to play a bigger role in automation as that technology continues to make advancements.
“AI enables all robots to learn from their own experience,” he says. “The goal of all our solutions is to be able to use AI in our automated systems more and more. Our goal — our mission — is to enable the industrial workforce through robotics. Not to replace humans, but to augment their capability.”
Brad Kramer is managing editor of Solar Builder.
Tags: automation, commercial and industrial, Sarcos Technology and Robotics Corp., solar robotics, Terabase Energy, utility-scale