Carports just make sense. Of the 21.4 GWs of solar installed in the U.S. to date, between 10% and 15% has been built on top of carports, according to Wood Mackenzie. Demand for this efficient use of space continues to surge — generating clean energy while shielding cars from the elements.
A 2012 study from the U.S. Geological Survey shows that parking lots cover nearly half-a-percent of America’s total land area — some 13,778 square miles. If we were to add PV atop that entire area, the U.S. would enjoy nearly 500 GW of additional capacity without impinging on land already dedicated to wildlife, agriculture, or housing.
More than 15 years ago, Terrasmart was among the first to begin installing large-scale solar canopy carport systems. So far, we have partnered on more than 270 MWs of canopy projects throughout the U.S. Our expert designers, architectural engineers, and knowledgeable project managers can help customers navigate the complex variables that go into building solar canopies on garage structures and surface parking lots.
The following two recently completed projects illuminate Terrasmart’s unique approach to creating cost and design efficiencies that streamline execution and value-engineer canopy projects.
You can also read more about these projects in this Terrasmart white paper.
Fresh Plant Solar Canopy
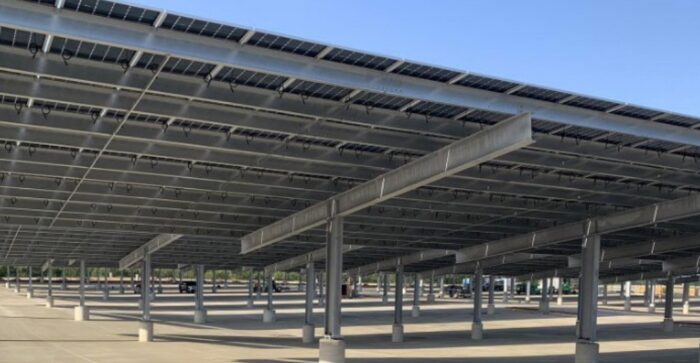
- Size 2.67 MW
- Location San Antonio, Texas
- Array Fixed tilt, 7° array tilt
- Canopy T-structure, 17 canopies
- Modules 5,496 qty, Qcells PEAK 485Wp
- Developer and EPC: Centrica Business Solutions
Fresh Plant is one of the largest independently owned food retailers in the country. Placing solar canopies on surface lot structures to produce clean energy aligned with the grocer’s commitment to public service,
environmental sustainability, and its employees — all in one go.
Challenges
Layers of local permitting approvals threatened to bog down the project. Also, Fresh Plant’s aggressive schedule and multiple subcontractors required exact sequencing and coordination among the entire team: from site grading, drilling, and pouring the concrete foundations to paving the entire parking
lot and ultimately installing the racking structures and modules.
Solutions
The complexity of such coordination required Terrasmart’s years of experience to smooth the way. Terrasmart’s project managers anticipated every move and kept the project ahead of schedule. While the details of this intricate project may have perplexed a less-experienced competitor, Terrasmart showed its strengths as the team successfully fabricated the racks exactly to specs and ensured on-time material delivery.
“We were under a lot of pressure to perform and make sure we didn’t delay any teams behind us. So we poured our foundations three weeks ahead of time,” said Saul Mendez, Terrasmart’s on-site project manager.
Results
Material savings | While the geotechnical report called for 24- to 36-inch diameter concrete foundations
at depths between 18 and 20 feet, Terrasmart’s designers were able to value-engineer the system using a 24-inch diameter and an 18-foot depth. This design required only two yards of concrete per foundation instead of five yards — a 60% materials reduction that provided a consequential savings across the project.
Zero change orders | Solar canopy projects are rarely completed with zero change orders. In fact, 95% of these systems experience on average 2% in change orders. In this case, though, the Terrasmart team delivered with no additional costs to the customer.
Turnbridge Parking Garage Canopy
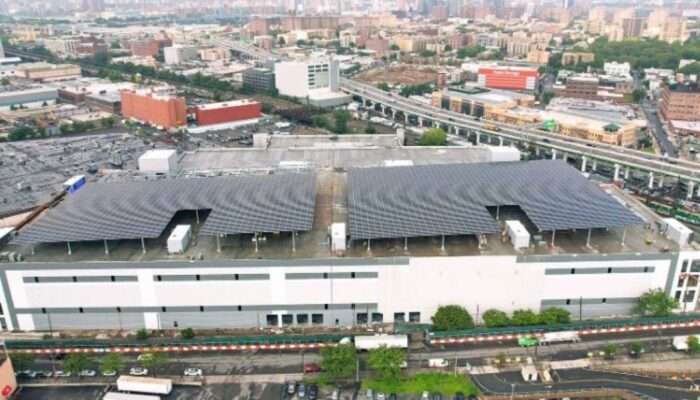
The 2.9-MW garage canopy system atop the Bronx Logistics Center (BLC) is one of New York City’s
largest private sources of renewable energy. This one had some huge challenges. Read all about the solutions and results right here.
Tags: carports, Terrasmart