Utilities across the country are managing intermittent renewable integration with varying levels of success — and with good reason. Meeting resource adequacy, reliability, and resilience is a complex business that requires flexibility and inventive solutions.
National Grid, which serves 20 million customers in New York, Rhode Island, and Massachusetts, is piloting an innovative program to increase distributed generation (DG) interconnections throughout its territory. Using renewables to better manage peak capacity constraints, National Grid and other utilities are testing how DG systems impact the grid at the substation level.
Called Active Resource Integration (ARI), National Grid’s program tests how much distributed solar substations can integrate without overheating the utility’s expensive equipment — and while reducing overall risk.
Because National Grid must have the flexibility to curtail projects as needed to maintain system reliability, participating developers receive collaborative support from the utility.
Nexamp is a major community solar project developer in the Northeast. For Nexamp, National Grid’s ARI experiment meant the opportunity to move their projects up in the interconnection queue while foregoing upfront engineering analyses, which can cost up to $1 million.
Nexamp submitted its 6.4-MW Allis Hill project in upstate New York for the ARI program. Half of the project’s output goes to a single large customer, while the other half serves the community solar system’s local subscribers.
Because National Grid’s program requires flexibility, and considering the snow, wind, and challenging soil conditions, Nexamp selected long-term partner Terrasmart to install its risk-mitigating ground screw foundations and supply the 1P tracker, while Phoenix Solar performed the mechanical and electrical installation.
“We trust Terrasmart to design and build a sustainable, reliable, low maintenance tracker system. If we know we are going to lose potentially 2.5% in a year because of the ARI’s curtailment, we don’t want to lose any additional money in repairs,” said Hugh Jones, project manager for Nexamp.
ARI program project planning and execution
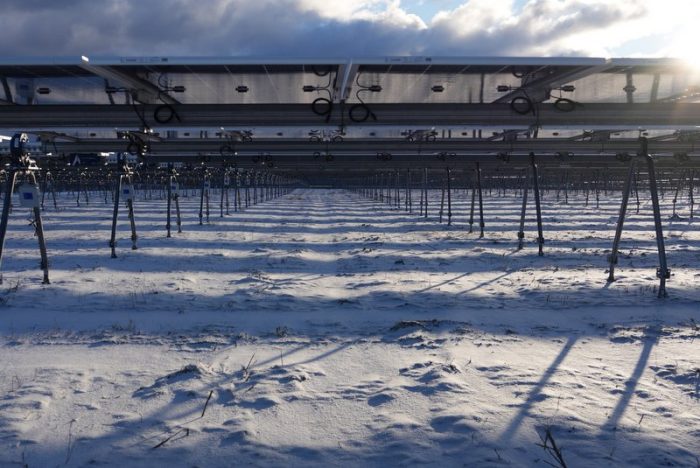
Project details
● Project Size: 6.4MW
● Location: Canastota, NY
● Start Date: 9/5/23
● End Date: ETA completion early April ‘24
● Foundation Type: 3,421 ground screws
● Rack Type: TerraTrak 1P
● Soil Type: Clay
● Frost depth: 42’’
● Wind loading: 101 mph
● Ground snow loading: 60 psf
● Wind and corrosion design life: 40 years
As one of the first to deploy ground screws in the U.S. solar market more than a decade ago, Terrasmart is renowned for its bankability in difficult terrain and weather. Terrasmart developed its proprietary ground-screw installation equipment based on its installers’ input from the field. Developers rely on those foundations to mitigate the risks of frost heave and challenging soils as they contend with the Northeast’s long winters and thaw/freeze cycles.
Specifically for the Allis Hill project, Terrasmart’s streamlined ground screw installation was a critical success factor. A job scope that called for 35 days was completed in just under three weeks.
Terrasmart’s team uses its own survey equipment to precisely stake each point before pre-drilling and driving ground screws. The bespoke equipment allows crews to navigate sites more efficiently with fewer personnel — only three operators on the site at any time.
The installation team actually exceeded its 175 screws per day goal, securing 200 screws each day with pinpoint accuracy. That boils down to one to two minutes for drilling and two minutes to install each screw.
Structural choice: TerraTrak 1P single-axis tracker with ground screws
Nexamp selected Terrasmart’s 1P SAT for Allis Hill, which required that the legs be set to a predetermined height. Terrasmart’s custom screw extensions and A-frames are designed to have up to 36 inches of adjustability, which means they can handle local undulations and variations in slope between the foundations.

The streamlined one-portrait configuration shares 80% of its parts with the two-portrait system, which has been proven in more than 500 MWs of projects in some of the most challenging conditions and terrain. Like the 2P, 1P is foundation-agnostic and can be paired with adjustable legs, allowing maximum flexibility both above- and below-grade.
The most significant benefit for Nexamp, however, is the tracker’s height and ease of installation. TerraTrak 1P’s lower profile is key in a state like New York where systems above a certain height require more stringent permitting. This makes the system even more attractive, both visually and administratively.

As an added bonus, the lower height meant ladders were not required during the installation. According to the Bureau of Labor Statistics, ladder-related falls account for 5,000 injuries per year in construction alone. For Nexamp, this was huge. Two installers are required to use ladders on a site — one at the bottom to spot and the other up top to secure the system. Because Allis Hill was installed during the winter with only a six-hour daylight window, the project could be completed much faster without that doubling-up.
“We were able to install 2,112 panels in one day and that’s an incredible figure,” said Kyle Moore, assistant project manager for Nexamp. “The main contributing factor for this speed is TerraTrak’s 1P low profile and accessibility from the ground. Our installers could handle a panel themselves, hang it on the system, bolt it and quickly move on. Not needing ladders increased safety and kept the team fully engaged in handling wires, bolts, racking and modules – all while reducing labor hours.”
TerraTrak’s streamlined cable management compounded the benefits. Aside from being able to wire the system from the ground, electricians didn’t need drip loops and other cabling because the system’s integrated cable channels run the wiring alongside the torque tube for a streamlined profile.
Once the portion of the foundation installation was complete, Terrasmart passed the remaining work (installation of the screw extensions, legs, torque tube, rails, and modules) over to Phoenix Solar, while continuing to support the process as a technical advisor to Nexamp. Terrasmart designed, manufactured, and fulfilled all of the project’s racking supply.
“In our industry where communication is sadly lacking, it’s such a breath of fresh air to work with Ron Dawkins, project manager for Terrasmart,” states Hugh. “Ron is incredibly detailed and proactive in his communication, even when it wasn’t good news. That takes a special kind of person.”
Tags: case study, Community Solar, Nexamp, Terrasmart