The solar industry recently welcomed the largest silicon solar cell manufacturing outfit to ever open its doors within the United States — the 3-GW factory operated by ES Foundry in Greenwood, South Carolina.
There have been many announcements by companies wanting to start solar cell manufacturing in the United States, but very few have made real progress since manufacturing tax credits were first included in the Inflation Reduction Act of 2022. Only one company started cell operations before the end of 2024 — Suniva in Norcross, Georgia. That factory had an easier start than others, considering the site had already manufactured silicon solar cells for nearly 10 years before shutting down in 2017. Suniva updated equipment and is once again supplying U.S. panel assembly plants with American-made PERC solar cells.
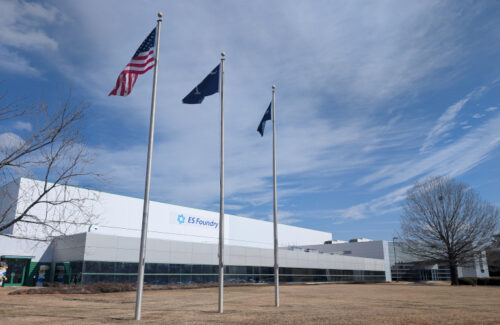
ES Foundry in South Carolina. Credit: Solar Power World
Now the country has its second cell factory, and its largest. Not only is ES Foundry producing more cells than Suniva (3 GW compared to Suniva’s 1 GW), but it’s approaching supply deals differently too. Whereas Suniva has gone the common route of initiating supply agreements with U.S. panel assemblers, ES Foundry is instead working with large-scale project developers and utilities to guarantee domestic content supplies. If a project needs American-made panels, ES Foundry will pen a three-way contract with the developer and their preferred module vendor. Although the partners were not publicly revealed, ES Foundry has already signed one of those three-way contracts in a multi-gigawatt supply agreement.
At ES Foundry’s ribbon cutting last week, domestic panel manufacturers, project developers and utilities were in attendance, eager to see the scale at which ES Foundry will soon be operating — product is rolling off the lines right now, and the company expects to reach 1 GW of manufacturing capacity by March and then 3 GW by August. Any amount of domestic cells is a hot commodity, ES Foundry CEO Alex Zhu told Solar Power World at the event.
“Domestic content is key,” he said. “Everyone needs the ITC, [especially] if it’s changed that you need domestic cells.”
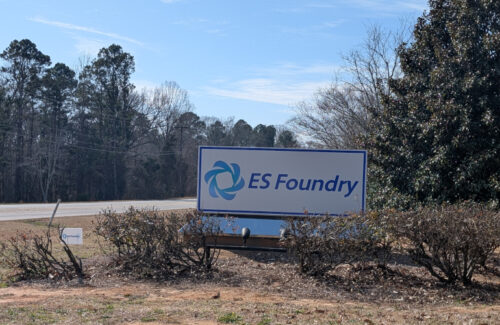
ES Foundry in South Carolina. Credit: Solar Power World
There are many questions surrounding President Trump’s support of the Inflation Reduction Act and its provisions that are supportive of domestic deployment and manufacturing of solar. One assumption is that the investment tax credit (ITC) will be updated to require domestic content to receive the full credit amount. And right now, the easiest way for solar panels to qualify as “domestic” is to use American-made cells.
ES Foundry is making bifacial PERC cells, a logical choice to avoid the unpredictable future of TOPCon panel production in the United States. The cells first start as gray silicon wafers and go through many steps on their seven-hour journey to finished product — things like diffusion, etching, oxidation, back passivation, plasma enhanced chemical vapor disposition and screen printing. The “diffusion” step is likely the most important, as that is when the dope paths (p- and n-type processes) are established. Only when the diffusion step is done on American soil can a solar cell be considered domestic-made and qualify for any domestic content advantages.
Zhu said that while the 4¢/W 45X manufacturing credit is a nice bonus for solar cell makers, ES Foundry is more concerned with meeting domestic content requirements for its end customers. That domestic content play is what will keep ES Foundry going while President Trump’s agenda is ironed out.
SPW visits the plant
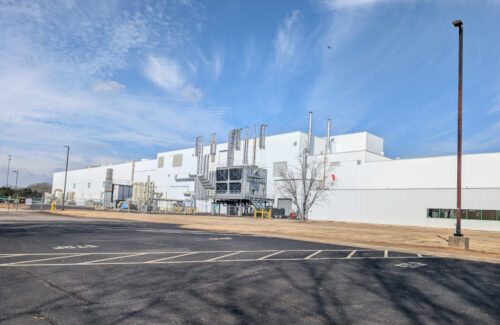
ES Foundry in South Carolina. Credit: Solar Power World
The first thing noticed upon approaching the ES Foundry building is the scale — the factory is large with gas offtakes coming off its sides. The “foundry” is in a former building used by Fujifilm to make inkjet paper and other photo products. Zhu said that the height of the Fujifilm building is what first attracted him to the space, as there aren’t many existing 70-ft tall manufacturing sites in America. Fujifilm occupied five stories of the building; ES Foundry knocked out four stories to make one large open space to accommodate chemical piping and manufacturing equipment. The building’s height could potentially accommodate silicon ingot pulling and wafering in the future, if financial aspects make sense, Zhu said. It would be unique to have a site ready to go and not rely on a green-build.
The difference between a panel assembler and a cell manufacturer is apparent at once. Solar panel manufacturers are assembling cells, backsheets, junction boxes and frames. Cell manufacturers are more chemical-focused and rely on a clean operation. Before entering the plant, workers (and visitors) have to don head-to-toe protective gear and walk through an air bath to remove airborne contaminates. Zhu said ES Foundry is able to source most of the chemicals used in manufacturing — phosphorus, silicon nitrate, etc. — in the United States, while, of course, the wafers, silver paste and aluminum paste are coming from Southeast Asia.
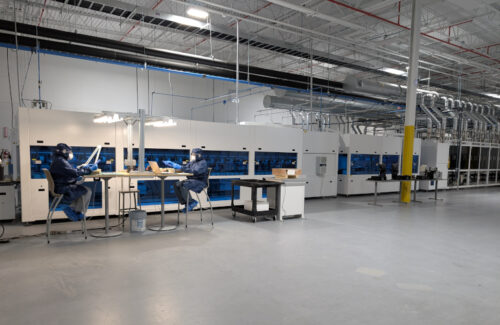
ES Foundry in South Carolina. Credit: Solar Power World
Besides finding a building that was the right height and equipped with significant electricity and wastewater hookups, ES Foundry was fortunate the local Greenwood workforce was already familiar with chemical processing. Ascend, a nylon polymer and fiber manufacturer just down the street, recently announced it was closing its doors. ES Foundry has already hired many former Ascend employees and is holding more job fairs locally. Construction on ES Foundry’s interior took just eight months, and 125 workers are now on the payroll. The company expects to have 300 employees by the end of March and 500 by Q3, which would make ES Foundry one of the largest employers in Greenwood.
This may be the year for more solar cell manufacturers to come online in the United States. Qcells is close to opening its wafer-cell-panel operations in Georgia and Silfab is still hopeful to begin cell manufacturing in South Carolina. Other companies like Boviet Solar (North Carolina) and Canadian Solar (Indiana) could begin silicon cell operations within the next 18 months. They will join Suniva and ES Foundry in the revitalization of the U.S. solar manufacturing industry — and not a minute too soon.
“The future begins now,” Zhu said, as ES Foundry executives officially cut the ribbon on the country’s largest solar cell manufacturing plant.